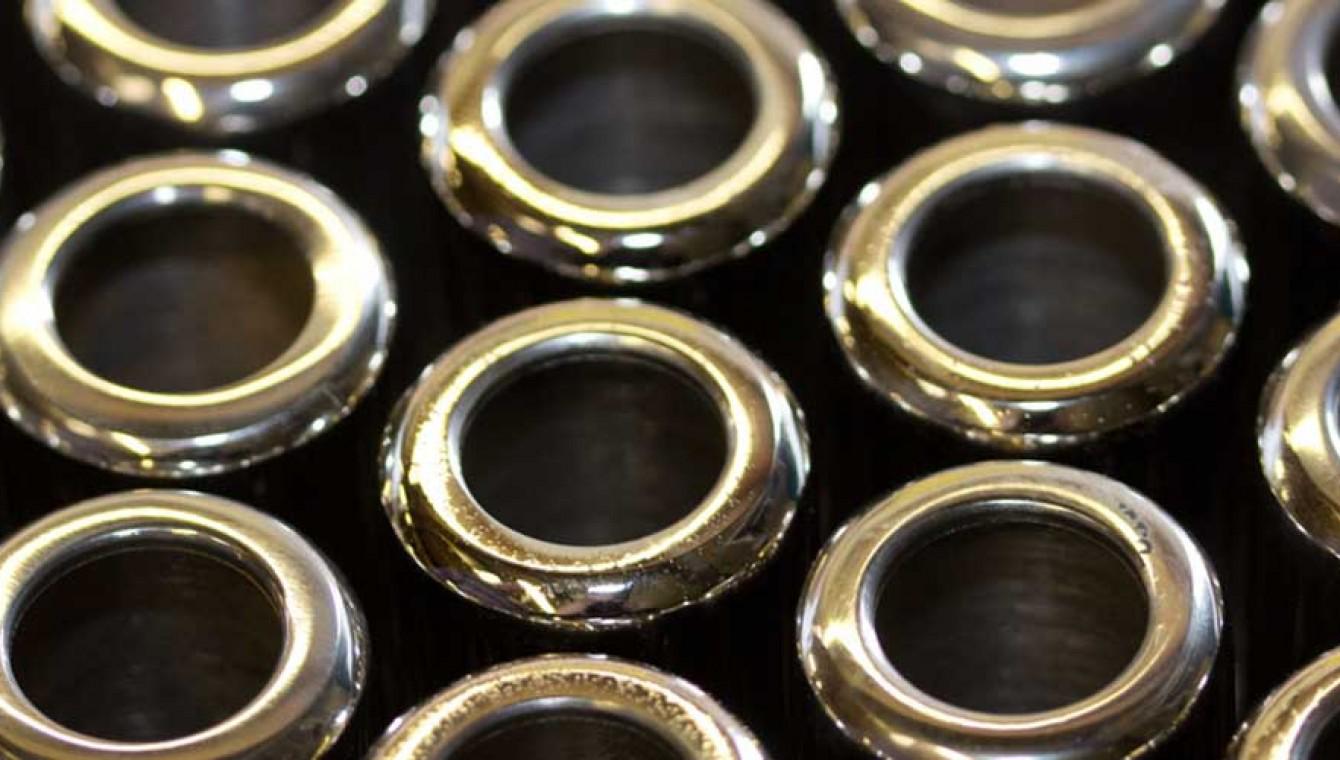
Electroplating of zinc alloy substrate:
Die-cast zinc alloy products have a wide range of applications, but due to the zinc alloy have low chemical stability, many zinc alloy die-casting parts require electroplating treatment to enhance anti-corrosion performance, and improve the appearance and value of the product at the same time. The most common combination electroplating with copper/nickel/chromium and various colored plating. Common zinc alloy die casting plating products include faucets, zipper pulls, belt buckles, buttons, luggage buckles, toys, locks, lampshade decorations and door handles, etc.
Requirements for zinc alloy electroplating:
The zinc alloy generally used for electroplating contains approximately 4% aluminum, and the aluminum content should not be too high, otherwise the adhesion of the electroplating layer will deteriorate. Before electroplating, the appearance of the zinc alloy die castings should be inspected for any defects. Some cosmetic defects can affect the quality of plating, such as cracks, cold shuts, shrinkage holes, hard spots, corrosion and blackening on castings.
Plating Standard for Zinc Alloy Substrate:
ASTM B456 Standard Specification for Thickness of Copper/Nickel/Chromium and Nickel/Chromium Electrodeposition Plating:
Service condition No. | Classification No. | Nickel thickness, um |
SC 5 | Zu/Cu5 Ni35d Cr mc Zu/Cu5 Ni35d Cr mp | 35 35 |
SC 4 | Zu/Cu5 Ni35d Cr r Zu/Cu5 Ni30d Cr mc Zu/Cu5 Ni30d Cr mp | 35 30 30 |
SC 3 | Zu/Cu5 Ni25d Cr r Zu/Cu5 Ni20d Cr mc Zu/Cu5 Ni20d Cr mp Zu/Cu5 Ni35p Cr r Zu/Cu5 Ni25p Cr mc Zu/Cu5 Ni25p Cr mp | 25 20 20 35 25 25 |
SC 2 | Zu/Cu5 Ni20b Cr r Zu/Cu5 Ni15b Cr mc Zu/Cu5 Ni15b Cr mp | 20 15 15 |
SC 1 | Zu/Cu5 Ni10b Cr r | 10 |
Taking SC5 Zn/Cu5 Ni35d Cr mp as an example, Zn represents zinc alloy substrate, Cu5 represents copper plating thickness of 5um, Ni35d represents double or triple level nickel plating thickness of 35um, Cr mpStands for microporous chromium plating.
Zinc alloy electroplating according to this specification can meet the SC5 service condition. The following table is the standard requirements of the Copper Accelerated Acid Salt Spray (CASS) and the ASTM B287 standard for acid salt spray for various service conditions.
Service condition No. | CASS ASTM B368 (Hours) | Acid salt spray ASTM B287 (Hours) |
SC 5 | 44 | / |
SC 4 | 22 | 144 |
SC 3 | 16 | 96 |
SC 2 | 4 | 24 |
SC 1 | / | 8 |
Pretreatment process for zinc alloy substrate:
There is a oxide layer on the surface of the zinc alloy after die-casting, and it is also coated with the release agent of molding. If the die-castings undergo mechanical polished. these may also be residual of wax. There substances will affect the adhesion of the electroplating layer, resulting in blistering after electroplating. Therefore zinc alloy requires pre-treatment to remove these substances before electroplating.
The pre-treatment process includes wax removal, degreasing and acid activation. The wax removal process is to place the workpiece in ultrasonic wax removal water to remove the polished wax on the workpiece. The degreasing process is to use alkaline degreasing water to remove oil, and its alkalinity should not be too high to avoid serious corrosion of the zinc alloy, otherwise it will cause blistering after electroplating. The purpose of acid activation is to remove the oxide on the surface and expose the base metal, the activation solution is generally 1 to 2% hydrofluoric acid or fluoride salt, and the concentration and time of the activation solution must be accurately controlled, otherwise the compact layer on the surface of the zinc alloy will be corroded.
The compact layer of zinc alloy die castings is generally only 0.05mm to 0.1mm thick on the surface, and the lower structure of the compact layer is relatively loose and even contains air bubbles. These loose structures are not suitable for plating, so beware to wear off the compact layer of the surface during mechanical polishing.
Cyanide copper primer:
Cyanide copper plating is the most commonly used on base coating for zinc alloys, although there are under studding to the use of cyanide-free copper plating, it is still not widely used in production. Cyanide copper plating has two major advantages: the first is that it has very good infiltration ability, even if a complex zinc alloy parts can be coated deep in copper, avoiding the undesirable adhesion plating caused by the displacement reaction. The second is its good adhesion to zinc alloy. It is important to note that cuprous cyanide and sodium cyanide content, i.e. the ratio of copper ions (Cu+) to free cyanide (CN-), need to be strictly controlled that is not to affect the adhesion of the coating and the dissolution of the anode. High sodium hydroxide content in electroplating solution will also reduce the adhesion of the coating.
Other additives such as Neochel solution are added to the common cyanide copper plating solution to improve anodic dissolution, and brighteners are used to achieve a smooth and flat surface of the casting.
According to ASTM B456 Standard Specification for Copper/Nickel/Chromium and Nickel/Chromium Electrodeposition Coatings, the thickness of zinc alloy copper plating layer needs to be at least 5um, and it is best to control the thickness between 7 and 10um in actual production, because the primer copper layer is too thin and it will easily cause electroplating blistering. According to the calculation of 2ASD current density and current efficiency of 70%, the plating speed is about 0.58um/min, and it takes about 17 minutes to plate 10um copper layer. In the case of barrel plating, the plating time required will be longer because the current density will be lower.
In terms of the control of the electroplating solution, it is best to test the metal copper, free cyanide and sodium hydroxide in the plating solution every day during production, and also to check the Baumé proportion of the plating solution, because the carbon dioxide in the air can be dissolved in the plating solution to become carbonate salt, reducing the current efficiency and even the electroplating speed. In case the carbonate salt is too high, it should be given appropriately treatment. In the electroplating processes, to avoid the copper layer deposited by the displacement reaction, the workpiece should be charged into the groove, especially when run in barrel plating, if the plating solution fails to penetrate deep into the rolling barrel in a timely manner, the copper layer adhesion obtained by the displacement reaction is very poor.
Acid copper plating:
In zinc alloy plating, the function of acid copper plating is to improve the brightness and flattening of the workpiece, but it can also be replaced by nickel plating, because nickel plating can also provide brightness and leveling effect. However, the cost of acid copper plating is lower than nickel plating.
If the electroplated workpiece needs to be nickel-free (nickel plating will be replaced by white copper titanium plating), such as zipper pulls, belt buckles, buttons and other products that have long-term contact with the human body, and require a bright electroplated finish, electroplating with acid copper become inevitable choice.
The acid copper plating solution is composed of copper sulfate, sulfuric acid and chloride ions, and the additives are mainly some organic substances such as surfactants and dyes, which are slowly decomposed into impurities during the electroplating process. At this point, adsorption treatment with activated carbon or filter carbon cores is required. In severe cases, hydrogen peroxide needs to be added to the plating solution for further treatment."
Multi-layer nickel plating:
The nickel layer is mainly used as a coating for anti-corrosion, and it can provide a bright and flat appearance. Nickel plating can be divided into semi-bright nickel, bright nickel and microporous nickel, which can be combined into single-layer nickel, double-layer nickel and triple-layer nickel plating according to the requirements of anti-corrosion.
Nickel plating solution (Watts nickel) consists of nickel sulfate, nickel chloride and boric acid, while additives are some organic substances. Like acid copper plating, it will slowly decompose during use and need to be purified.
The Couloscope is used to measure potential differences, but also to measure the thickness of the coating Image (source by Fischer).
Commonly used nickel plating combinations:
Single layer nickel: Bright nickel
Double layer nickel: Semi-bright nickel + Bright nickel
Triple layer nickel: Semi-bright nickel + Bright nickel + Microporous nickel
Anti-corrosion ability: triple-layer nickel> double-layer nickel> single-layer nickel
The basis of the anti-corrosion ability of the three-layer nickel is explained: the potential of the bright nickel coating is lower than that of the semi-bright nickel coating, and when the corrosion reaction occurs, the coating with lower potential will corrode first, that is, the bright nickel will start to corrode first, so as to protect the lower coating and substrate from corrosion. According to ASTM B356 Standard Specification for Copper/Nickel/Chromium and Nickel/Chromium Electrodeposition Coatings, the standard range of potential difference between bright nickel and semi-bright nickel is 100 mV to 200 mV, and the potential difference can be measured and monitored using a Couloscope.
The microporous nickel coating is divided into many tiny non-conductive particles, which are used to disperse the current of the corrosion reaction, reduce the corrosion current and disperse the corrosion point. The thickness of microporous nickel only needs to be less than 1um, and according to ASTM B356 standard specification for copper/nickel/chromium and nickel/chromium electrodeposition coatings, the number of micropores is at least 10,000 points/10mm², which is not observable with the naked eye。
Enlarged image of the microporous nickel surface after treatment
(Image source: Atotech)
Metallographic cross-section of zinc alloy copper/nickel/chromium plating
(Image source: Promet)
Bright chrome plating:
The main purpose of chrome plating is to enhance the anti-corrosion ability of the product, and because the color of nickel plating is yellowish, chrome plating can give a whiter and brighter color. According to ASTM B356 Standard Specification for Copper/Nickel/Chromium and Nickel/Chromium Electrodeposition Coatings, the minimum thickness of the bright chrome coating is 0.25um (except for SC1, which is at least 0.13um, see the next part of the SC explanation). Due to the poor positioning ability of chromium (the ability to coat metal in the low current density area) and the high internal stress, the entire chrome layer should be evenly divided as much as possible to avoid cracks in the high current density area, which may lead to failure of the salt spray test.
The composition of the bright chrome plating solution is simple, only chromic acid and sulfuric acid, but the ratio of chromic acid and sulfate has a great impact on the positioning ability of the plating solution, so it requires a strict control.
Because the current efficiency of chromium is very low (only about 13%), a large amount of hydrogen will be produced during the electroplating process, which can bring out carcinogenic hexavalent chromium into the air and affect human health. In addition, due to the accumulation of a large amount of oxygen, if there is a spark that can lead to an explosion, an effective exhaust system must be installed on the cylinder side. The bright chrome plating solution can also be added with a displacement agent as required.