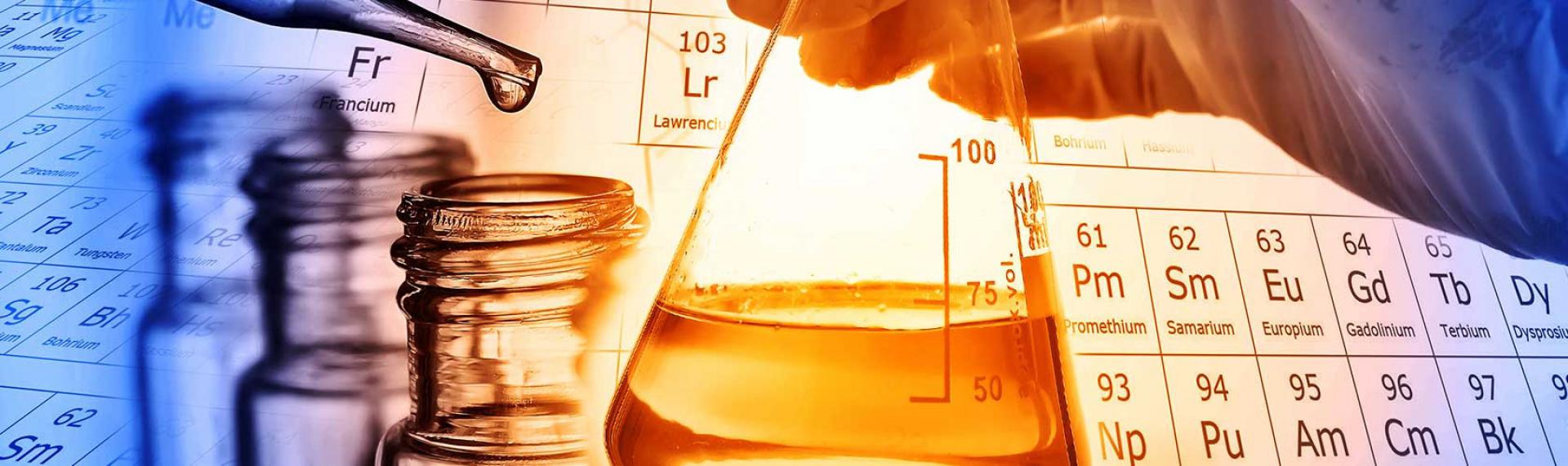
In the alloy manufacturing and die-casting industry, the chemical composition of raw materials and finished products is one of the most important factors in providing high-quality products. To obtain accuracy data, spark optical emission spectrometry (SPARK-OES), inductively coupled plasma atomic emission spectrometry (ICP-OES) and, increasingly, portable X-ray fluorescence spectrometry (XRF) are commonly used in the industry for composition testing. What are the advantages and disadvantages of each assay and its cover range?
1. Inductively Coupled Plasma Atomic Emission Spectrometry (ICP-OES) – extremely accurate for measuring substances at low concentrations
The principle of ICP-OES is to atomize the sample solution through a nebulizer, and then enter the inductively coupled plasma at about 10,000 degrees Celsius for freeization, in this process, all elements will produce their specific spectral lines, and the higher the ion concentration, the stronger the intensity of light, and then use the detector to measure. ICP-OES is extremely accurate and suitable for measuring substances at low concentrations, down to the ppb level. However, the equipment cost is high, and the sample needs to be liquefied, which will be more inconvenient on operation.
2. Spark Optical Emission Spectrometry (SPARK-OES) – fast, efficient and widely used in metal product measurement
The principle of SPARK-OES is similar to that of ICP-OES, except that the excitation source of SPARK-OES is a "spark", which is generated by the electrode and the sample to excite the atoms and release a unique spectrum, which is then detected and measured by an observer. Although less accurate than ICP-OES, the equipment cost is lower, and there is no need to prepare samples into solutions, so most manufacturers use SPARK-OES for quality control purposes.
3. Portable X-ray fluorescence spectrometer (XRF) – inexpensive, fast, and easy to control
XRF is based on the principle of irradiating a sample with high-intensity X-rays, which are excited by the X-rays energy absorption, emitting the fluorescence spectrum unique to the elements themselves. Depending on the intensity of the wavelengths, the type and amount of elements contained in the sample can be analyzed.
ICP-OES and SPARK-OES are both destructive tests that require sample preparation prior to testing, so more companies are looking to introduce more convenient and faster testing methods to improve work efficiency, and one of the more common is portable X-ray fluorescence spectrometer (XRF). Portable XRF is convenient, fast, inexpensive, requires no sample preparation, and is not a destructive test compared to the two traditional technologies, which does improve the efficiency of the work.
What are the limitations of portable XRF assays?
Theoretically, XRF can be analyzed quantitatively and qualitatively, but only under extremely tight conditions.
- The wavelengths emitted by certain elements can interfere with each other and cause detecting error, which requires analysis by professionals and is not easy for ordinary operators.
- X-ray sources generally produce a single electromagnetic radiation and excite specific elements, so it is necessary to select the appropriate X-ray source for different samples.
- Portable XRF is also only suitable for the detection of high-altitude sub-order elements (higher atomic number than sulfur(S)) because the low atomic number of elements emits lower fluorescence energy and is easily absorbed by the air before reaching the sensor, thus not obtaining accurate data. Due to the low atomic order elements (e.g., aluminum, magnesium, etc.) in zinc/aluminum alloys, they are particularly unsuitable for portable XRF.
- If the thickness of the sample is less than 10mm, there will be serious errors in the detection value of some elements;
- Test time also has a significant impact on the accuracy of XRF, and if only qualitative testing is performed, ten seconds may be good enough. However, if a quantitative test is required and reaches the ppm level, it will take 10 minutes or more, otherwise the test results will not be accurate.
| Portable XRF | SPARK-OES | ICP-OES |
Equipment costs | Lower | middle | high |
Sample preparation time | Extremely short | short | long |
The lab test takes time | Very short (qualitative) / | short | long |
Precision | middle | high | Extremely high |
Destructive testing | not | be | be |
The range of elements suitable for inspection | Elements with atomic order greater than | Elements that | Elements that |
Summary:
Portable XRF is generally only used for qualitative testing, to initially check whether certain elements are present in a sample, or whether the content of such elements is high or low, and is not suitable for accurate quantitative testing, and for issuing product analysis reports (CAs) or acceptance.