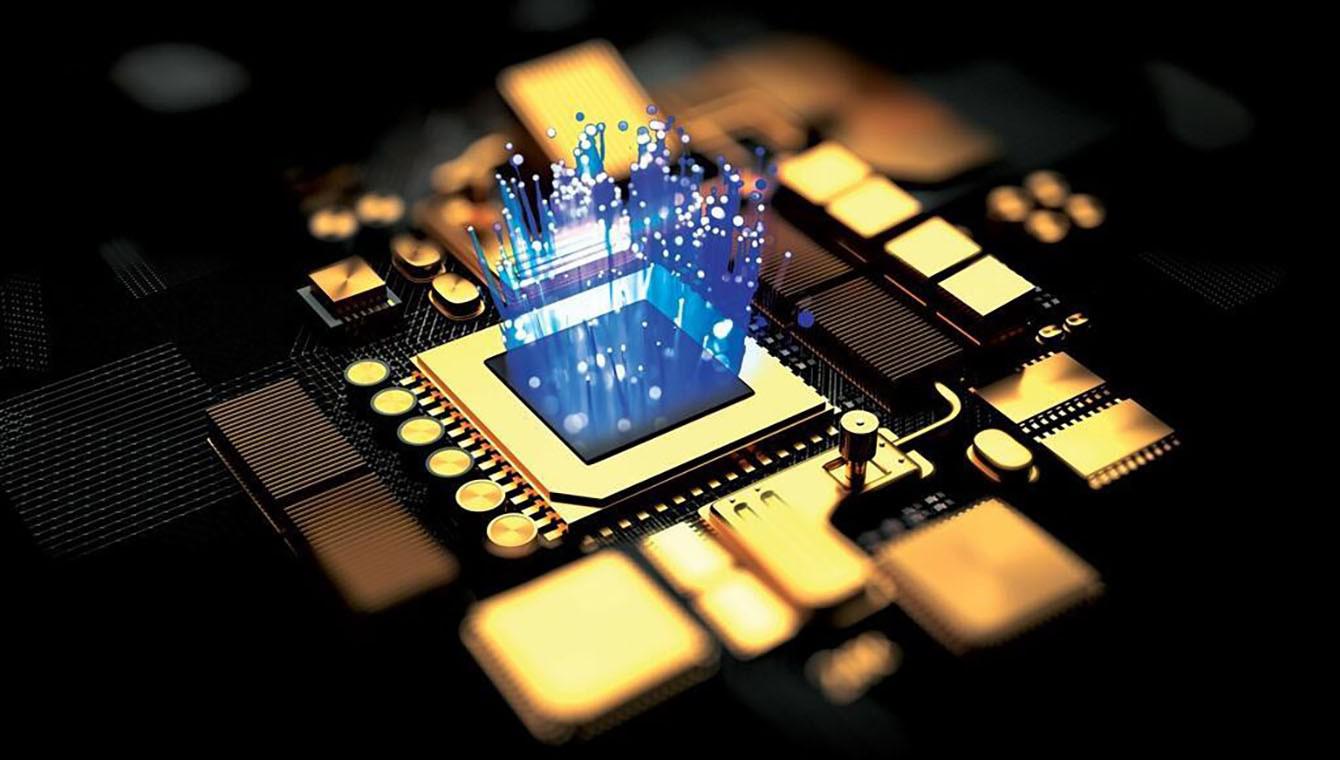
Nowadays, most communication equipment is transmitted by optical fiber and cable. As the terminals send and receive data as the electrical signals, the optical modules have become an indispensable device for photoelectric signals conversion at both ends. The optical module market is expected to grow rapidly in recent years, during to increasing investment in new data centers and the adoption of more expensive high-speed modules by cloud service providers, as well as expanded the development of 5G networks by global telecommunications.
In general, the chassis and cover of the optical module are made of die-casting, which has the advantages of high dimensional accuracy and low processing cost, so it is the most commonly applied in manufacturing of the optical module production. Traditional alloys for optical module die casting include No. 3, No. 4, and No. 5 zinc alloys, as well as A360, A380, ADC10, and ADC12 aluminium alloys.
Limitations of traditional alloys:
Due to the design of optical module requires for Thin-Wall die casting, although the fluidity of No. 3, No. 4 and No. 5 zinc alloys is relatively good in the commonly used zinc alloys, there are still defects such as pin holes, shrinkage, and gas porosity in general die casting, as a result lower pass yield rate outcome in electroplate processing. Many die-casting factories also solve the above defects by increasing the pressure, mold temperature and furnace temperature, at the same time, it also causes another problems such as mold sticking and tooling erosion.
Due to the 5G network has faster transmission speed and the higher power consumption compared to 4G, the cooling factor for the equipment are most important and required higher performance. However, most of aluminium alloys are generally produced from recycled aluminium, which has a high content of impurities, and its thermal conductivity is not much improvement compared with zinc alloys (see Table 1).
material | A360 | A380 | ADC12。 | 3# zinc alloy |
Thermal conductivity W/m.K | 113 | 109 | 96 | 113 |
Table 1: Comparison of the thermal conductivity of commonly used aluminium alloys and No. 3 zinc alloys
Challenges faced by optical module die casting:
In addition to the common problems of pin holes, gas porosity, mold sticking and tooling erosion in the die-casting process, because the optical module chassis is a thin-walled design with a complex structural, it is relatively prone to the problem of cold shuts, which is mainly related to the product structure, mold temperature, material temperature, filling mode, pressure and flow rate, injection conditions and alloy fluidity.
Figure 1: Cold shut
Other than that, the draft angle of the optical module is small, and some area of the die casting is too thick, caused there with high mold temperature, so it is easy to have the problem of mold sticking. This refers to the accumulation of zinc metal on the surface of the mold, once more liquid metal flow into the mold, causing damage to the mold surface. However, cooling water insufficiency, uneven application of release agents, and lack of spray cooling in hot areas can all lead to mold sticking.
Figure 2: Mold erosion problem
In order to improve the filling effect of the mold cavity and reduce the generation of cold shut, many optical module die-casting factories will adopt the method of reducing the gate width and increasing the die-casting pressure to improve these defects, but high pressure and flow rate are also easy to cause mold erosion. The mold surface is damaged by the repeated impact of metal flow and forms a sink, which may cause more serious strain and sticking to the mold, and the life cycle of the tools will be reduced. Small flange wrinkle is visible on the surface of the product. Since erosion can occur in any liquid flow. When a vortex is formed, some near-vacuum air porosity or cavities are created. And it will travel with the metal flow until burst. This blasting process can generate extremely high pressures (up to hundreds of MPa) in a very small area, impacting the die surface and ultimately causing an explosion.
In order to minimize the occurrence of accidents, it is important to properly handle the problem of mold erosion, for example, by using a lower flow rate at inner gate; The temperature of the molten metal should not be too high; Avoid abrupt cross-sectional changes of the runner, and the cross-sectional area should be large to small; Increase the jet angle and try to avoid directly impact on the molding part; Optimization of exhaust effect during filling, etc.
Figure 3: Sticky mold problem
A special alloy for problems solving of optical module die casting applications.
In view of the current problem that traditional zinc alloy and aluminium alloy cannot effectively cooperate with the application of optical module die-casting products, special alloys came into being. Special alloys include special zinc alloys and special aluminium alloys, which are designed to meet the special requirements of optical module die casting and improve the characteristics of traditional zinc alloys and aluminium alloys, that effectively solve the challenges faced by optical module die casting.
Special zinc alloy
MDX and MDX² smartphone-based photoelectric special zinc alloys
MDX and MDX² retain the advantages of zinc alloys, such as excellent die-casting properties, mechanical properties, and improved fluidity, which can not only effectively improve the problem of pin holes and cold shut, but also reduce the sticking mold and mold erosion, and are more suitable for thin-walled products. The material has less impurities, the gradual electroplating and surface treatment effect is more ideal, coupled with its good electromagnetic shielding performance, the casting can win with stability. MDX and MDX² zinc alloys are specially designed for the optical module industry, MDX² is the first choice for products in the intelligent optoelectronic industry, covering optical module housings, optical communication connector components, high-end audio-visual external connector components, thin-walled electronic parts, etc.
| Ultimate tensile strength (MPa). | Yield Strength (MPa). | Elongation (%) | Hardness (HB). |
MDX | 310 | 225 | 8 | 88 |
MDX² | 320 | 225 | 5 | 90 |
No. 3 zinc alloy | 283 | 221 | 10 | 82 |
No. 5 zinc alloy | 328 | 228 | 7 | 91 |
Table 2: Comparison of the performance of MDX vs. MDX2 vs. No. 3 and No. 5 zinc alloys
Note: The production process of tensile bar is die-casting
Special aluminium alloy
Aluminium castings with a wide range of applications, so there are many special aluminium alloys designed for the characteristics of their applications. Manufacturers can choose according to the specific application of the product.
AD8A extra-strong high thermal conductivity aluminium alloy
“AD8A” die-casting aluminium alloy is modified by unique contents and manufacturing technology for increasing the thermal conductivity, which not only has the stable and good casting process of general aluminium alloy, and also makes the electrical and thermal conductivity of the casting better and more stable than the aluminium alloy with similar performance on the market, which is suitable for the products with high quality requirement such as transmitting antennas, middle frame of mobile phone, optical module housings, LED lighting accessories and radiators.
specification | A360 | A380 | AD8 | AD8A |
Conductivity %IACS | 30 | 27 | 33~40 | 37~45 |
Table 3: Conductivity comparison of AD8A with conventional aluminium alloys
Note: The conductivity of different castings has slightly performance.
AD3 corrosion-resistant aluminium alloy
AD3 aluminium alloy combines excellent corrosion resistance with good heat dissipation and fluidity without the need for surface treatment. Its die-casting performance is similar to ADC12, and it can be die-cast into a variety of complex structural parts, especially suitable for outdoor electronic products, outdoor furniture, sports equipment, etc., which require high stability.
Table 4: Salt spray testing of AD3 compared to conventional aluminium alloys.
ADC12X high-strength high-duralumin alloy
The ADC12X is designed for mobile phone middle frame, with unique contents and manufacturing processes that allow it to meet the specifications of the ADC12 while remaining lightweight, while achieving higher strength and hardness. Its excellent fluidity makes it readily apply to many manufacturers of mobile devices, drone parts, high-strength structural parts and thin-walled products.
| Ultimate tensile strength (MPa). | Shear strength (MPa). | Elongation (%) | Brinell hardness (HB). |
ADC12 | 265.5 | 144.7 | 1.67 | 118.5 |
ADC12X | 308.6 | 167.8 | 1.64 | 128.9 |
Difference | 43.1 | 23.1 | -0.03 | 10.4 |
Difference ratio | 16.23% | 15.96% | -1.80% | 8.78% |
Table 5: Performance comparison of the ADC12X and the ADC12
AD12 low coefficient of thermal expansion aluminium alloy
Optoelectronic products attach great importance to precision, such as self-driving car cameras, but many applications are difficult to avoid temperature differences, and a high coefficient of thermal expansion of the product will increase the error and reduce the reliability and durability of the product. The AD12 has a low coefficient of thermal expansion and is designed for professional grade optical accessories.
specification | ADC12 | AD12 |
Coefficient of thermal expansion (20~100°C, um/mm/°C). | 21 | 18 |
Table 6: Comparison of the coefficient of thermal expansion of AD12 and ADC12
Conclusion
To keep up with the technological speed of optical module industry and keep abreast with the times, many manufacturers are actively using innovative materials and adopting expert opinions to improve their processes, that enhance their competitiveness and lead the industry. The special alloy for optical module die-casting can effectively help manufacturers improve product quality, reduce defects, improve production efficiency, and bring outstanding quality, performance and good value to optical module die-casting products.